Selecting the Right Wire Rope
Thousands of wire ropes of all different types, sizes, and construction are manufactured throughout the world, and the differences in these ropes have a dramatic effect on strength and operating characteristics. Because of their differences, wire rope selection can be a very difficult task for someone without basic wire rope knowledge.
Although it would be impossible to list the correct rope to use on each crane for every application, the following information will teach you the basics to selecting the right rope. Keep in mind, if there is ever a question about which rope to use, it is always best to consult a wire rope expert.
Access the Equipment
Whether it is a crawler crane, rough-terrain crane, truck crane, tower crane, pedestal crane, or boom truck, the first task is to make sure the selected rope meets the OEM's requirements for diameter and strength. Next, find out the specific make and model of crane, as well as what type of application the crane and rope will be used in.
It's also important to note whether the rope will be used as the main hoist, auxiliary hoist, trolley rope, boom hoist, or luffing jib boom hoist, which makes a major difference in the type and construction of rope you will use. To further complicate wire rope selection, if the machine is older, the rope used may depend on its mode of failure on the machine and application. I'll touch on that again a little later.
Once the make, model, application, diameter, and required rope strength is known, then the process to select the rope can be started.
Main and Auxiliary Hoist Ropes
Main and auxiliary hoist ropes can be either conventional six- or eight-strand or rotation-resistant ropes. If the application does not require a rotation-resistant rope, then a conventional rope should be used.
The category of rotation-resistant rope to be used in any application depends primarily on length of fall. If the maximum boom length and length of fall is within the scope of a six- or eight-strand conventional rope, then a rotation-resistant rope in not required. However, if a rotation-resistant rope is required, there are three different categories of rotation-resistant rope to choose from.
These three categories have significant differences in strength, rotation resistance, and operating characteristics. It is extremely important to match the requirements of the crane with the specific characteristics of the rope selected. The following is some basic information on the three categories of rotation-resistant rope.
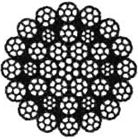
Category 1
- At least 15 outer strands.
- Highest strength and most rotation resistant.
- Can be used with a swivel.
Category 1: Endurance Dyform 34LR
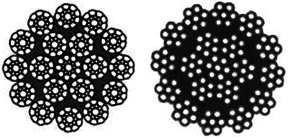
Category 2
- At least 10 outer strands.
- Medium strength and rotation resistant.
- Should not be used with a swivel.
Category 1: Endurance Dyform 18 (left) & Endurance 19x7
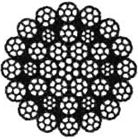
Category 3
- No more than outer strands
- Lowest strength and rotation resistant.
- Should not be used with a swivel.
Category 3: Endurance 8
Boom Hoist Ropes
Boom hoist ropes have some very unique and specific requirements. The ASME B30.5 standard allows boom hoist ropes to be used at a design factor of 3.5:1 with a minimum bending ratio of 15:1. Primarily because of these factors, rotation-resistant ropes are not allowed to be used as boom hoist ropes. The only exception is that a luffing jib boom hoist rope may be a rotation-resistant rope if used at a design factor of 5:1 and bending ratio of 18:1.
Boom hoist ropes typically must be resistant to crushing on the drum, and this requirement makes compacted strand or compacted ropes a good choice on some cranes. However, compacted ropes may not be appropriate for all boom hoist rope applications because they have improved resistance to crushing, but they do not have the same fatigue resistance as compacted strand or conventional ropes.
Compacted strand wire rope: Endurance Dyform 6 (left) and Endurance Dyform 8
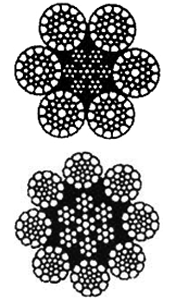
Environmental Conditions
For most applications, environmental conditions will not require special rope or lubrication. Most mill-applied lubricants also will operate at a fairly wide temperature range of -40° F to 120° F and will provide sufficient anti-corrosion properties to operate in most environments.
Almost all ropes will be required to be lubricated in service. A light penetrating lubricant is recommended, as opposed to grease or an otherwise heavier lubricant. A field-applied lubricant should penetrate into the interior of the rope but also not be too thick or dark, so it will not inhibit visual rope inspection.
Abrasion Resistance Vs. Bending Fatigue Resistance
While there is a possibility, there is little likelihood that an application can be found for which there is a precisely suitable wire rope–one that can satisfy every indicated requirement.
As with all engineering design problems, feasible solutions demand compromise to some degree. At times, it becomes necessary to settle for less than optimum resistance to abrasion in order to obtain maximum flexibility; the latter being a more important requirement for the given job.
A typical example of this kind of trade-off would be in selecting a highly flexible rope on an overhead crane. Conversely, in a haulage installation, a rope with greater resistance to abrasion would be chosen despite the fact that such ropes are markedly less flexible.
Two compelling factors that govern most decisions as to the selection of a wire rope are abrasion resistance, and resistance to bending fatigue.
Striking a proper balance with respect to these two important characteristics demands judgment of a very high order. A graphic presentation of just such comparison of qualities between the most widely used rope constructions and others is given by means of X-chart.
Referring to this chart when selecting a rope, the mid-point (at the X) comes closest to an even balance between abrasion resistance and resistance to bending fatigue. Reading up or down along either leg of the X, the inverse relationship becomes more apparent as one quality increases and the other decreases.
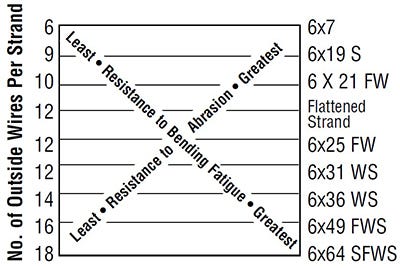
The Wire Rope industry refers to this as the X-Chart. It serves to illustrate the inverse relationship between abrasion resistance & resistance to bending fatigue in a representative number of the most widely used wire ropes.
Effect of Sheave Size
Wire ropes are manufactured in a great variety of constructions to meet the varying demands of wire rope usage. Where abrasion is an important factor, the rope must be made of a coarse construction containing relatively large wires.
In other cases, the great amount of bending to which the rope is subjected is more important. Here, a more flexible construction, containing many relatively small wires, is required.
In either case, however, if the rope operates over inadequate size sheaves, the severe bending stresses imposed will cause the wires to break from fatigue, even though actual wear is slight. The smaller the diameter of the sheave, the sooner these fatigue breaks will occur and the shorter rope life becomes.
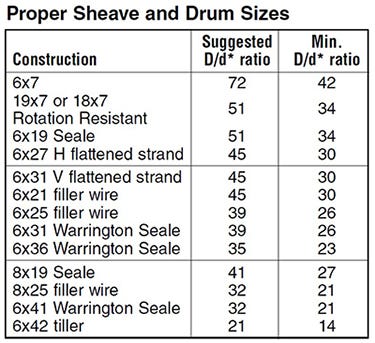
*D = Tread Diameter of Sheave / d = Nominal Diameter of Rope
Another undesirable effect of small sheaves is accelerated wear of both rope and sheave groove. The pressure per unit area of rope on sheave groove for a given load is inversely proportional to the size of the sheave. In other words, the smaller the sheave the greater the rope pressure per unit area on the groove. Both sheaves and rope life can obviously be prolonged by using the proper diameter sheave for the size and construction of rope.
Sheave diameter can also influence rope strength. When a wire rope is bent around a sheave, there is a loss of effective strength due to the inability of the individual strands and wires to adjust themselves entirely to their changed position. Tests show that rope strength efficiency decreases to a marked degree as the sheave diameter is reduced with respect to the diameter of the rope.
Therefore, it is evident that a definite relationship exists between rope service and sheave size. As a guide to rope users, wire rope manufacturers have established standards for sheave sizes to be used with various rope constructions. To secure the most economical service, it is important that the suggested size of sheaves given here be used.